When selecting a hydraulic or pneumatic quick coupling, one key performance factor often overlooked is pressure drop. Whether you’re connecting hydraulic implements on a tractor or linking pneumatic tools in a workshop, pressure drop can impact system efficiency, speed, and performance.
What Is Pressure Drop?
Pressure drop refers to the reduction in pressure from the inlet to the outlet of a component—in this case, a quick coupling—when fluid or air flows through it. This happens due to internal restrictions, turbulence, and friction inside the coupling.
Too much pressure drop can result in:
- Reduced actuator speed
- Lower flow rates
- Increased energy usage
- Heat buildup
In simple terms, more pressure drop means your system is working harder to move less fluid.
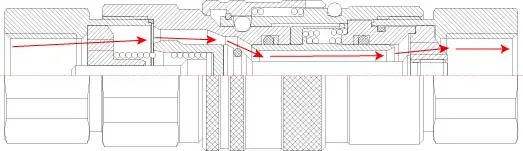
Factors Affecting Pressure Drop in Quick Couplings
Several variables influence pressure drop:
Internal Design
- Couplings with more internal components (like poppet or ball valves) have higher restriction.
- Ball valves usually has lower Pressure Drop than the Poppet Valve.
- While flat-face couplings are known for easy cleaning and leak prevention, they don’t inherently have more pressure drop than ball-type couplings due to more internal surface area. In fact, flat-face couplings are often designed to minimize internal friction and thus minimize pressure drop.
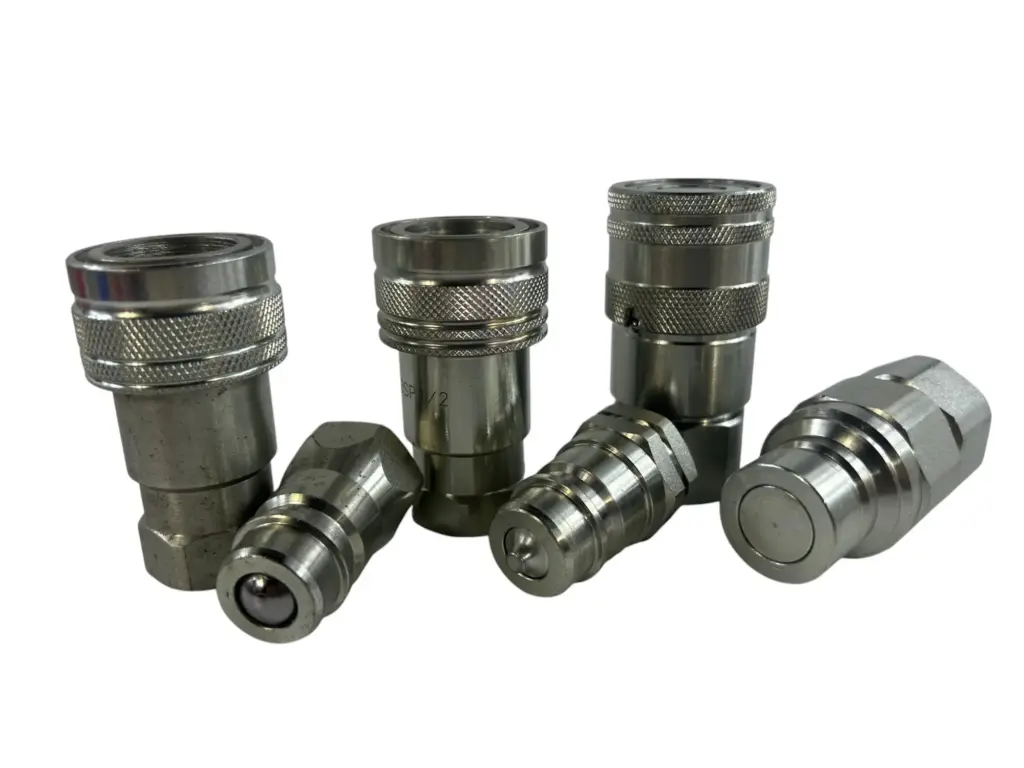
Bore Size
- The larger the internal diameter, the lower the pressure drop (assuming the same flow rate).
- Smaller sizes increase resistance and turbulence.
Flow Rate
- Higher flow rates naturally create more pressure drop. Pressure drop often increases exponentially with flow rate.
Connection Type and Condition
- Worn or dirty couplings increase turbulence.
- Mismatched or damaged connectors may restrict flow.
Typical Pressure Drop Data by Coupling Type and Size
Here’s a general reference of pressure drop (ΔP) values in bar or psi at a flow rate of 25 L/min (6.6 GPM) for hydraulic couplings:
Coupling Type | Size | Pressure Drop (Approx.) |
---|---|---|
ISO 7241-1 Series A | 1/4″ | 1.2 bar (17 psi) |
ISO 7241-1 Series A | 1/2″ | 0.3 bar (4.5 psi) |
ISO 7241-1 Series A | 1″ | 0.08 bar (1.2 psi) |
ISO 7241-1 Series B | 1/4″ | 1.0 bar (15 psi) |
Flat Face ISO 16028 | 3/8″ | 0.6 bar (9 psi) |
Flat Face ISO 16028 | 1/2″ | 0.4 bar (6 psi) |
Push-to-Connect (Steel) | 1/2″ | 0.5 bar (7 psi) |
Note: These values can vary depending on the brand, specific design, and materials. Always refer to manufacturer data sheets for precise numbers.
How to Minimize Pressure Drop
- Choose the correct size: Don’t undersize your coupling—match it to your system’s flow requirements.
- Select the right coupling type: Ball-type couplings typically allow higher flow with lower drop than Poppet Valve; flat face couplings are better for cleanliness and leak prevention and special improved Minimal Pressure Drop.
- Use high-quality couplings: Precision machining and smooth internal surfaces help reduce turbulence.
- Maintain your system: Dirt and wear increase pressure drop. Always keep couplings clean and replace damaged parts.
Real-World Example: Tractor 3rd Function Kit
When using a 1/2″ ISO A quick coupling in a tractor’s 3rd function kit to run a grapple, a high pressure drop might slow the cylinder’s response time. Upgrading to a larger 3/4″ coupling or a different type with less restriction (like an ISO B or flat face) could improve response speed and reduce heat in the hydraulic system.
Conclusion
Pressure drop is more than a technical term—it directly affects the performance of your hydraulic or pneumatic system. By understanding how coupling type and size affect flow resistance, you can choose the best quick coupling for your application and maximize efficiency.
Need help selecting the right coupling for your system? Feel free to reach out—we’re here to help.